Projects
REWE Logistic center -Magdeburg
Swisslog spearheaded the installation of a state-of-the-art ACPAQ solution at REWE's logistics center in Magdeburg. This ambitious project involved the implementation of an entirely new infrastructure. From pallet conveyor systems and cranes to depalletizing robots, a case buffer in a cyclone carrier, a reshuffler in the conveyor system, a palletizing robot, and tray loading/unloading capabilities, every component was carefully integrated to create a cutting-edge logistics setup. The result is a fully modernized facility that has revolutionized REWE's operational efficiency and productivity.

Rexel Logistic Center -Lyon
Rexel's new warehouse in Lyon showcases an innovative setup designed to enhance efficiency and streamline order fulfillment. The facility features an Autostore installation, an advanced robotic system that optimizes inventory management. Additionally, a cutting-edge conveyor system is in place to create carton boxes, which are then filled with orders by skilled operators. To complete the packaging process, carton closer machines are employed, and label and notice printers ensure accurate order information. Finally, a network of shipping conveyors ensures smooth transportation of the packaged orders. This state-of-the-art solution empowers Rexel to deliver orders swiftly and effectively, meeting the demands of their customers with precision and speed.
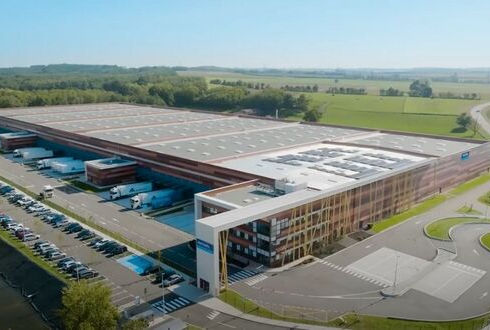
Johnson&Johnson Logisitic Center- Courcelles
​Johnson & Johnson's project in Courcelles marks a significant upgrade to their existing logistics infrastructure. The old Savoye system has been replaced with a cutting-edge conveyor system provided by Swisslog. This comprehensive solution encompasses various components such as Autostore, a state-of-the-art robotic system that optimizes storage and retrieval processes. Additionally, carton erector and closing machines ensure efficient packaging, while shipping printers generate accurate labels for outbound shipments. A sorter conveyor facilitates the seamless movement of goods, and an inbound buffer enhances overall operational efficiency. With this advanced system in place, Johnson & Johnson's logistics operations in Courcelles are primed for improved productivity and enhanced customer satisfaction.

Volvo - Gent
​Volvo's project in Gent involves the installation of the latest hardware versions in the car body buffer warehouse's three cranes. This comprehensive upgrade includes state-of-the-art components such as the newest frequency inverters for all axes, advanced sensors for improved precision and safety, and cutting-edge programmable logic controllers (PLCs) for efficient control and monitoring. By incorporating the latest hardware versions, Volvo ensures that their cranes in Gent are equipped with the most advanced technology available, resulting in enhanced performance, reliability, and overall efficiency in their car body buffer warehouse operations.

CoolBlue Logistic Center - Tilburg
Coolblue's project in Tilburg involves a significant expansion of their existing warehouse facilities. The expansion includes the implementation of a new Autostore system and an advanced conveyor system. The conveyor system comprises several key components, starting with an inbound area dedicated to filling the Autostore bins with goods. The outfeed area features carton erection and closing machines to streamline the packaging process. Additionally, a labeling machine ensures accurate labeling of packages, while a shipping labeling system facilitates efficient shipment preparation. Finally, a transfer conveyor seamlessly connects the new system to the existing sorter, ensuring smooth transition and integration between the two. With this expansion project, Coolblue aims to enhance their storage capacity, optimize order fulfillment processes, and ultimately provide an improved experience for their customers in Tilburg.

GICA-new Cement Line -SIGUS
The SIGUSFA project represents a significant milestone in the cement industry, as thyssenkrupp industrial solutions constructed a new 600 tpd cement line for GICA Group. This expansive project encompasses various critical components to ensure efficient cement production.
The project includes a new raw material crushing area, where materials are processed to meet specific requirements. A dedicated raw material stocking area facilitates smooth material handling and storage. The inclusion of a raw vertical mill optimizes the grinding process, while a kiln and polytrack system ensure precise and controlled cement clinker production.
To further enhance the production process, a cement ball mill is incorporated to finely grind the clinker, preparing it for final use. A comprehensive conveying system efficiently transfers the cement to silos for storage. Additionally, an expedition installation facilitates the loading and dispatch of cement products.
To support this advanced infrastructure, the SIGUSFA project boasts modern controls and an engineering room equipped with the latest technologies. A fiber optic network ensures reliable and high-speed communication throughout the facility, promoting seamless coordination and monitoring of operations.
The SIGUSFA project is a testament to the collaboration between thyssenkrupp industrial solutions and GICA Group, introducing a state-of-the-art cement production line that exemplifies innovation, efficiency, and advanced engineering in the industry.
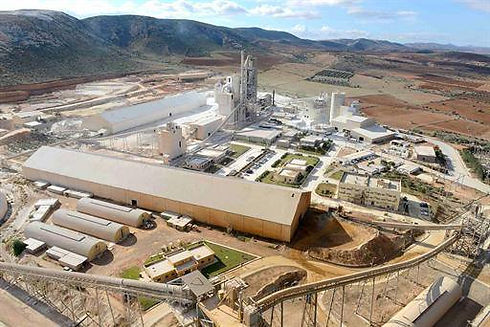
JALLA GAZ04- Tunis
The Jalla Gaz project, undertaken by Methania, represents an innovative solution for transforming biogas derived from cow waste into electricity. This sustainable system incorporates a range of sophisticated components to ensure efficient and reliable energy production.
At the heart of the project lies a complex instrumentation system, carefully designed to monitor and control the biogas transformation process. This instrumentation enables precise measurement of key parameters such as gas composition, temperature, and pressure, ensuring optimal system performance.
The Jalla Gaz project also features a modern Human-Machine Interface (HMI) that provides operators with intuitive control and real-time visualization of the system's operation. The HMI enhances user experience, facilitating efficient monitoring, troubleshooting, and process adjustments as needed.
Furthermore, the project utilizes advanced Programmable Logic Controller (PLC) software, which acts as the brains of the operation. The PLC software enables seamless integration and coordination of various system components, ensuring smooth operation and optimizing energy generation.
Together, the complex instrumentation, modern HMI, and PLC software form a robust and intelligent system for transforming biogas into electricity. The Jalla Gaz project showcases Methania's commitment to sustainable energy solutions, harnessing the potential of cow waste to produce clean and renewable electricity while utilizing state-of-the-art technology for efficient control and operation.
.jpg)
QNCC new cement line - Qatar
The QNCC project is a remarkable achievement in the cement industry, as Fives FCB has constructed a new 5000 tpd cement line in Umm Bab, Qatar, for the Qatar National Cement Company. This ambitious project encompasses various essential elements to ensure efficient and sustainable cement production.
The project includes a state-of-the-art raw material crushing area, where materials are processed to meet specific quality standards. A dedicated raw material stocking area facilitates smooth handling and storage of the materials. The incorporation of a raw vertical mill optimizes the grinding process, while a kiln and Cooler system ensure precise and controlled cement clinker production.
To further enhance the production process, a cement mill is integrated to finely grind the clinker, preparing it for final use. A comprehensive conveying system efficiently transfers the cement to silos for storage. Additionally, an expedition installation facilitates the loading and dispatch of cement products.
The QNCC project embraces modern controls and an engineering room equipped with cutting-edge technologies. A fiber optic network ensures reliable and high-speed communication throughout the facility, promoting seamless coordination and monitoring of operations. Furthermore, a process historian server is employed to log essential data and generate automated daily reports, providing valuable insights into production performance and enabling data-driven decision-making.
The QNCC project exemplifies the commitment of Fives FCB and the Qatar National Cement Company to sustainable and efficient cement production. Through the integration of advanced technologies and comprehensive infrastructure, the project sets a new benchmark in the industry, ensuring optimal performance, quality, and operational excellence.
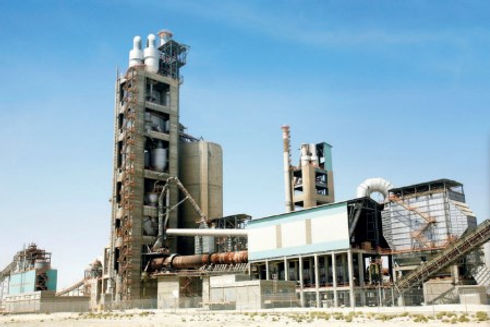
GICA new cement line - Ain Kebira
The Kebifa project stands as a remarkable achievement in the cement industry, with thyssenkrupp industrial solutions constructing a new 6000 tons per day (tpd) cement line for the GICA Group. This extensive project encompasses a range of essential components to ensure efficient and sustainable cement production.
The project features a new raw material crushing area, meticulously designed to process materials to meet stringent quality requirements. A dedicated raw material stocking area facilitates organized handling and storage of the materials. Incorporating a raw vertical mill optimizes the grinding process, while a kiln and polytrack system ensure precise and controlled cement clinker production.
To further enhance the production process, a cement ball mill is integrated to finely grind the clinker, preparing it for final use. A comprehensive conveying system efficiently transfers the cement to silos for storage. Additionally, an expedition installation streamlines the loading and dispatch of cement products.
The Kebifa project is equipped with modern controls and an engineering room featuring cutting-edge technologies. A fiber optic network ensures reliable and high-speed communication throughout the facility, promoting seamless coordination and monitoring of operations. Furthermore, the project includes a new lab facility and an expert system, enabling operators to generate accurate setpoints based on data analysis and expert recommendations, thereby optimizing production efficiency and product quality.
The Kebifa project exemplifies the commitment of thyssenkrupp industrial solutions and the GICA Group to advanced and sustainable cement production. With its state-of-the-art infrastructure and innovative technologies, the project sets a new standard in the industry, ensuring superior performance, precision, and operational excellence.

LAFARGE ALSAFWA new cement line - Jeddah
The ALSAFWA project represents a significant achievement in the cement industry, with thyssenkrupp industrial solutions constructing a new 6000 tons per day (tpd) cement line for the LAFARGE Group in Jeddah. This comprehensive project encompasses a range of crucial elements to ensure efficient and sustainable cement production.
The project features a state-of-the-art raw material crushing area, designed to process materials to meet rigorous quality standards. A dedicated raw material stocking area facilitates efficient handling and storage of the materials. Incorporating a raw vertical mill optimizes the grinding process, while a kiln and polytrack system ensure precise and controlled cement clinker production.
To further enhance the production process, a cement ball mill is integrated to finely grind the clinker, preparing it for final use. A comprehensive conveying system efficiently transfers the cement to silos for storage. Additionally, an expedition installation streamlines the loading and dispatch of cement products.
The ALSAFWA project includes modern controls and an engineering room equipped with cutting-edge technologies. A fiber optic network ensures reliable and high-speed communication throughout the facility, promoting seamless coordination and monitoring of operations.
The ALSAFWA project exemplifies the commitment of thyssenkrupp industrial solutions and the LAFARGE Group to advanced and sustainable cement production. With its state-of-the-art infrastructure and modern technologies, the project sets a new standard in the industry, ensuring superior performance, efficiency, and operational excellence in the Jeddah region.

Cement de Bizerte- cement line - Bizerte
The Cibimod project signifies a significant advancement in the cement industry as Thyssenkrupp Industrial Solutions undertakes the renewal and replacement of the old cement line for Les Ciments de Bizerte company. This comprehensive project introduces a new and modern cement line, revolutionizing the production process.
The project encompasses various essential components starting with a new raw material crushing area, designed to process materials to meet precise specifications. A dedicated raw material stocking area ensures efficient handling and storage. The inclusion of a raw vertical mill optimizes the grinding process, while a kiln and polytrack system guarantee precise and controlled cement clinker production.
To further enhance the production process, a cement ball mill is integrated to achieve fine grinding of the clinker, preparing it for final use. A comprehensive conveying system efficiently transfers the cement to silos for storage. Additionally, an expedition installation streamlines the loading and dispatch of cement products.
The Cibimod project incorporates modern controls and an engineering room equipped with cutting-edge technologies. A fiber optic network ensures reliable and high-speed communication throughout the facility, facilitating seamless coordination and monitoring of operations.
The Cibimod project exemplifies Thyssenkrupp Industrial Solutions' commitment to advancing the cement industry by implementing state-of-the-art infrastructure and modern technologies. With the introduction of this new and modern cement line, Les Ciments de Bizerte company can expect enhanced performance, efficiency, and operational excellence in their cement production operations.
