Optimize Automated installations to support operation Growth
- nidhal ben soltane
- Jun 21, 2023
- 2 min read
If everything is running smoothly and ‘as expected’ at an automated plant, it may feel like there isn’t much need for a system operations team. But look below the surface.
In most cases, achieving a state where everything is running smoothly is due to the hard work of not just the system operations team, but also teams of technicians and maintenance staff, from both the automation provider, and the client.
Having an advanced automated system delivery maximum benefit is a bit like a Formula 1 engine – it will give you top performance, but pitstop team have to keep it tuned, and have to jump on any problem and fix it ASAP. Companies often falter is putting in place an effective service and maintenance program that helps maintain consistent peak operational performance from the automation system.
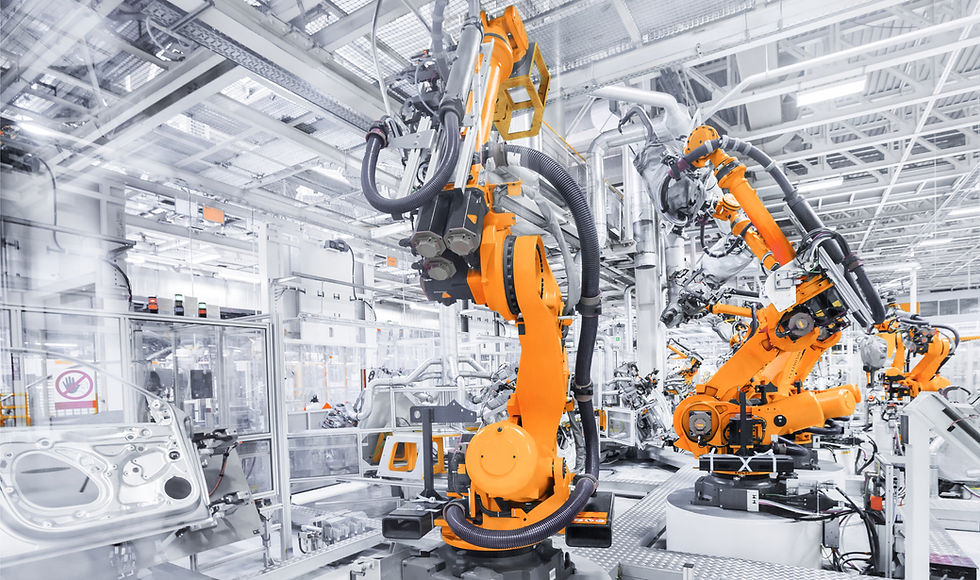
This can be especially challenging in today’s environment where companies are struggling with the challenges of meeting rapidly changing customer demands while navigating through an unprecedented labor shortage.
An inadequate or ill-equipped service and maintenance effort could hinder the performance of plant automation systems, creating a serious vulnerability in the supply chain. All it takes is one neglected or missed issue to worsen for the automation system to experience unplanned downtime. This in turn could delay product fulfillment and tarnish the customer experience.
Understandably, many companies that typically rely on in-house technicians or maintenance teams are struggling to maintain the level of service needed to help avoid performance reductions with automation technology. The labor shortage is making it difficult to recruit and retain the needed skilled technicians to support a proactive service and maintenance program.
At a time when there is unprecedented pressure on supply chain efficiency and uptime, there is growing concern that many in-house teams may not have the capacity or expertise to maintain the systems and adequately identify and remedy issues before they result in costly unplanned downtime.
For instance, below is a sample of what should be done.
· Training programs to enhance the competencies of the team and encourage safe working habits. The customizable programs are designed to enable staff to quickly identify and resolve issues, enhance long-term performance and retain important skills that could be lost from employee turnover.
· Dedicated on-site personnel, trained to operate, maintain and recover errors, who remain on-site to manage the maintenance of the equipment from installation to ongoing mechanical and software maintenance and upgrades to help alleviate the stress of employee turnover and allow the team to focus on core business functions.
· Condition monitoring that allows to view the current state of the automation system to ensure it is working at maximum efficiency, while also predicting possible problems to reduce the risk of unscheduled downtime. Feedback on how the automation solution is performing are documented and communicated out on a regular basis.
· The ability to replace obsolete or outdated parts with a newer version has been a key to continued high level service. The new parts are not always a direct ‘like for like’ swap. On many occasions, it’s necessary to either make an electrical, mechanical or programming change to support the installation of a new replacement part.
When it comes to maintaining and servicing automation solutions for long life and performance, it’s important to have the right people, strategies and results the operations needs.
Comments